25+ years ago I was splitting my time between a job where I was a scanner operator and an apprenticeship with a master printmaker. In the printmaking studio we were making large digital negatives on an imagesetter and using them to make hand-coated platinum/palladium prints in a wet darkroom. Back then everyone was using Photoshop 2 and had CRT monitors. While the color scans coming off the Leaf45 seemed pretty decent after a little color correction in curves, I was frustrated with how different the handmade B&W platinum palladium prints looked in comparison to the same images onscreen. We had developed curves to linearize the imagesetter that made the negatives but still, the prints on Arches Cold Press paper looked soo much different than they did onscreen. The paper had a warm tone that was darker and more yellow that what I saw onscreen. And the platinum palladium blacks were much lighter and warmer than the deep neutral blacks we saw onscreen.
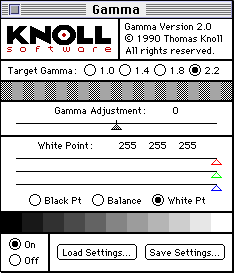
One day in the early 1990s I decided there had to be a way to fix this problem. I launched the Knoll Gamma Control Panel and made radical adjustments to the black and white points to match our wet darkroom platinum palladium printing process. I had been using Knoll gamma for a while but had never attempted to make such radical adjustments like matching the paper color and gentle blacks of a 19th century printing process. With just a minute’s worth of work I was able to get an astonishingly excellent match! All of the sudden, everything on screen looked like platinum palladium prints – even email! I saved these settings for platinum palladium and made another set of settings for the 4 color press work I was doing at my other job.
I was so excited about “monitor matching” that I started going around to everyone I knew adjusting their monitors to match whatever printing process they were working with. I learned to adjust the RGB gain, brighness and and contrast settings on their CRT monitors before doing the final tweaking in Knoll gamma.
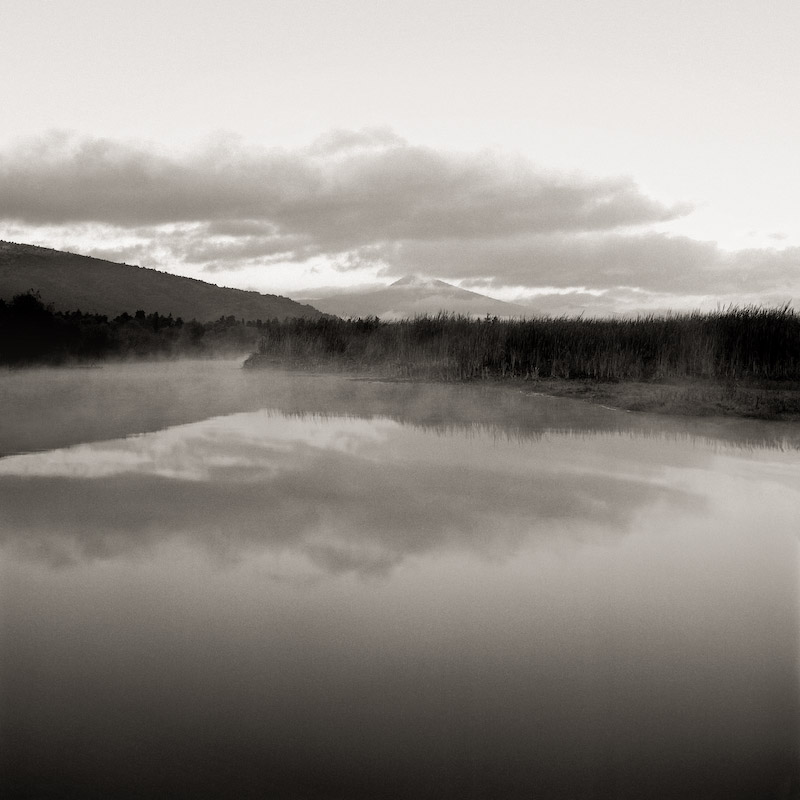

Before I know it, I was getting phone calls from complete strangers in advertising agencies, print shops and service bureaus asking if I could visit them and match their monitors. I started charging for this service in 1994 and have been doing it ever since. I became a drum scanner operator shortly afterwards using the world’s first drum scanner that supported RGB scans in addition to CMYK. Scanning in RGB was a revolutionary concept that I loved because I could better correct the images and convert them to a custom printer color space that I had created. Before I knew it, I was getting phone calls from places like New York, Iceland, London, etc from people that wanted to get the same scanner and hire me for a few days of training. In the late 90s, Photoshop 5.0 brought ICC profiles to the masses and devices like the MC7 and Colortron took things to the next level and the color consulting work became a demanding 60+ hour a week full time gig for me. That was when I created the Onsight name for the business I had already been doing for years.
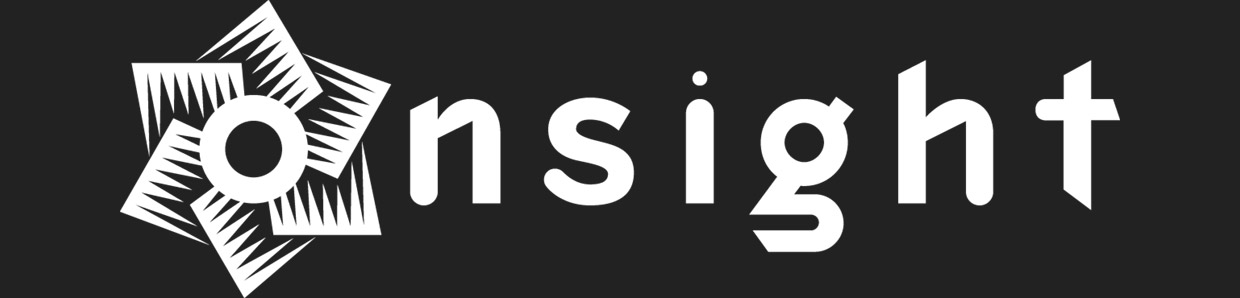

In 2012 we pioneered a simple method for calibrating and profiling alt-photo processes like platinum palladium, photo gravure, etc. We did this by bridging the gap between handlheld measurement spectrophotometers like the i1Pro and the greyscale profiling technology developed by Roy Harrington who makes the QTR line of products. Roy has since developed some curve smoothing algorithms and this is still the best way to calibrate alt-photo processes.
In the last few years we’ve been able to tweak the lighting, camera profiling and workflow for fine art reproduction. I’ve helped dozens of studios and museums redesign their lighting setup for perfectly even illumination with zero reflectance. And profiling there cameras with Basiccolor Input with a tweaked Capture One or Lightroom RAW workflow allows for quantifiable colorimetric accuracy. When combined with custom made media compensation curves, we can truly shoot-and-print without manual color corrections and get as accurate a reproduction as the media allows. This has been a revolution for those in fine art reproduction.
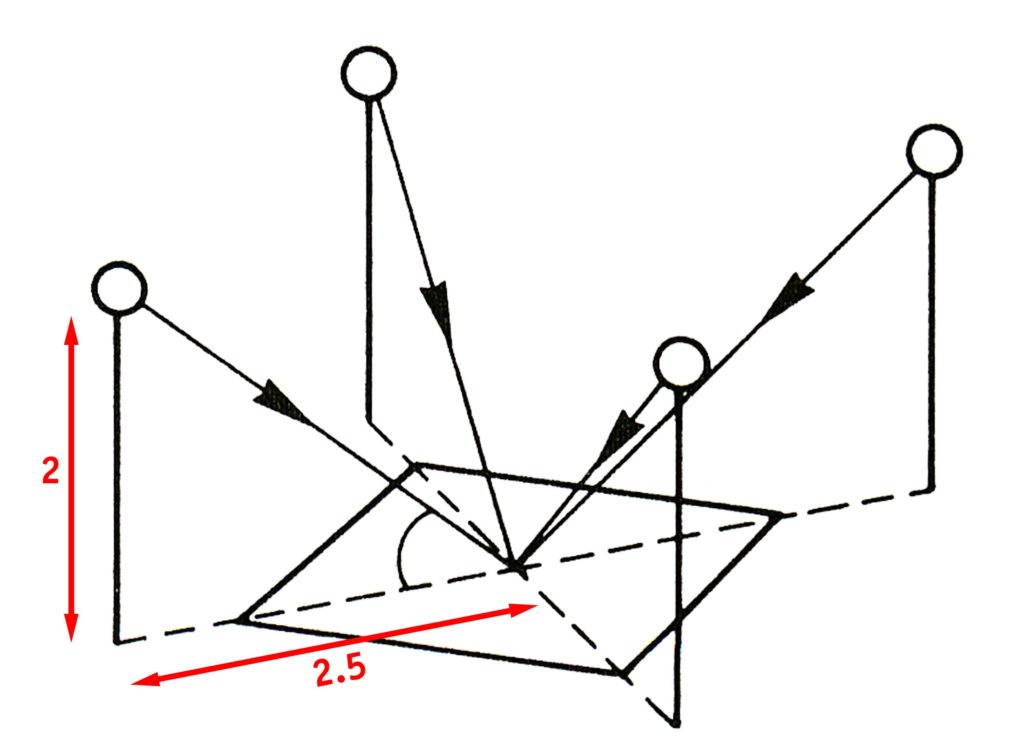
So this year, Onsight is celebrating 25 years of onsite digital imaging insight. It hass been a fun ride. I have worked with just about every printer ever made, on every RIP. I have had the chance to travel a lot of the globe and get to know so many people. Today I have a diverse client base that I support remotely in between occasional onsite visits. I’ve also been fortunate enough to be a beta tester for a variety of the developers creating the software and hardware in the business. I also found a fun niche working with media companies and the coating scientists that are developing coatings for processes like latex and dyesub.
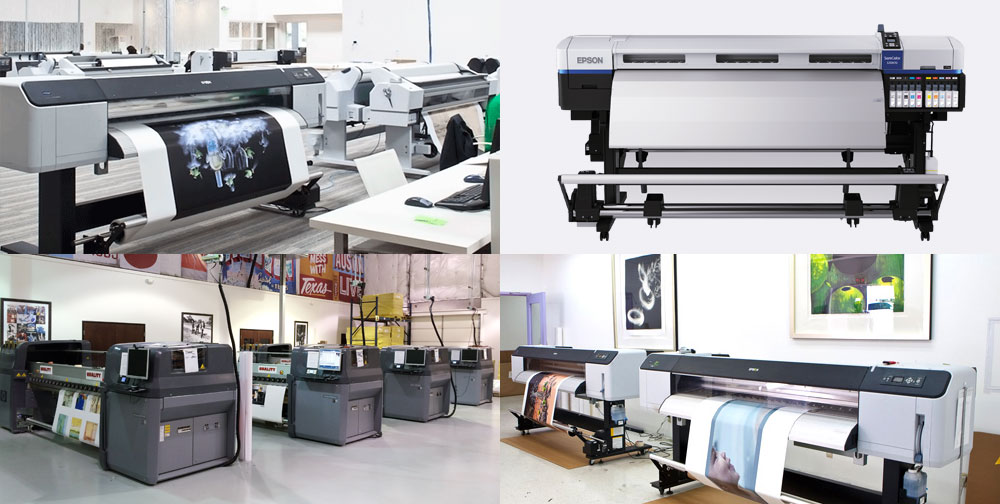
Looking forward, the RIPs that large format printers use still have a lame calibration and profiling process. The profiles that ship with these printers still aren’t great. Users of these printers tend to endure much less than perfect image quality. People are always shocked at how much better their prints look once I have calibrated and profiled them onsite. Because the color science in these RIPs is so poor, I have developed my own methodology for determining optimal ink limits, linearization curves and total inks limits outside of the RIP. I call it the ChromaMax calibration method. It helps us achieve optimal image quality with minimal ink usage, and give my clients a competitive advantage over their competition
I don’t call myself a ‘color management consultant’ anymore because there’s so much more to what I do than just manage color. I help people make beautiful prints. I talk a lot about how to approach grain and how important it is when printing. I help people think about the presentation of their prints. I help people reorganize massive Lightroom databases. I help strategize backup and archiving options. I help people tweak their whole workflow from start to finish. Elegance and simplicity go hand in hand with integrity, sustainability and peace of mind. A few smart decisions made today will ensure success down the road.
– Scott Martin